Buying the Machine
When you’re talking about impulse buys, then this is the one. I was having lunch and watching Ebay. I eventually stumbled onto a advertisement about a old mulcher. I opened the ad and watched the photo’s. Turned out this mulcher had extremely heavy flails. In my opinion this was a bush mulcher which is a super heavy machine to mow down complete forests. Dad and i hopped in the car, and took a look at the machine. The guy who had it only had a 60hp Same, which could not lift the machine, and neither power it higher then 300rpm. We decided we buy the machine, loaded it on the trailer and drove home.
Once home we gave it a go with the case quantum 95N tractor and tried it on some heavy pear branches. we gave it full throttle at the 540 rpm PTO, but not much happened to the wood. I was looking at the machine and the PTO seemed like a 1000rpm one. We swapped to 1000rpm and gave it full throttle and now the machine sounded unreal, and smashed everything into pieces.
Click here to display content from YouTube.
Learn more in YouTube’s privacy policy.
I straight away decided that i wanted a boom mechanism on the machine so it would push high bushes to the back, and never have them drop onto the cab of the tractor. So i started to measure, and construct this mechanism
Click here to display content from YouTube.
Learn more in YouTube’s privacy policy.
When i got the push mechanism finished we decided to shred some 20 year old orchard with the machine, and we also did a 50 year old pear orchard of a by now ex-collega which all worked out great. the trees got smashed into small chips.
The machine itself had a orange and rust color, which i did not like that much already. During Spring of 2020 i took the machine apart, and figured out a color what to paint the machine in. I disassembled everything but the mulch axle itself and cleaned and painted all the parts. some weld work was required here and there. The machine got the new color Antracite Grey with Machine green which turned out a nice combination.
The new paint
Click here to display content from YouTube.
Learn more in YouTube’s privacy policy.
In the end of 2022 we shredded alot of wood with our mulcher and it was starting to perform bad, but also cause alot of loud vibration. It was about time to get some new teeth on this machine. I could have ordered the original ones, but i decided i get a retrofit factory come by, and we looked at the machine and figured we could weld fixed bits on there which have alot more power. So we ordered these base parts with exchangeable widia tips so we couls smash our trees way better, but also have the machine go through the ground a bit deeper. I spent about 2 weeks for this project because the welding was a really big job, and had to be done perfectly. I used base electrodes to weld the base parts on, and balanced everything out by measurement, and eventually on the forklift to see if i had inbalance.
When taking the axle out i found out that the bearings where also broken. And these are super heavy bearing with 130mm outside, and 60mm wide spherical bearings. these are for sure the most expensive bearings on the farm with a allowed impact force of 400Kilonewton.
Click here to display content from YouTube.
Learn more in YouTube’s privacy policy.
The Unbalance issue
When trying the machine a while later we realised we did have very bad vibrations in the machine. The machine wasn’t perfectly in balance before the new knives and bearings, but it got worse after installing this all new. I had to do something about it as this vibration was quite destructional to the machinery and ourselves.
I had no idea at first how to get started on this and tried some stuff with slowmotion videos and markings on the rotor but this didn’t work and i couldn’t see the vibration well enough. In theory a accelerometer would be able to measure the acceleration in the Z-axis when the machine runs, so i searched arround the internet and found analog accelerometers which sample over 1Khz which should be fine to prevent aliasing when i spin the machine up to 2200 rpm which results in a frequency of about 37,7Hz.
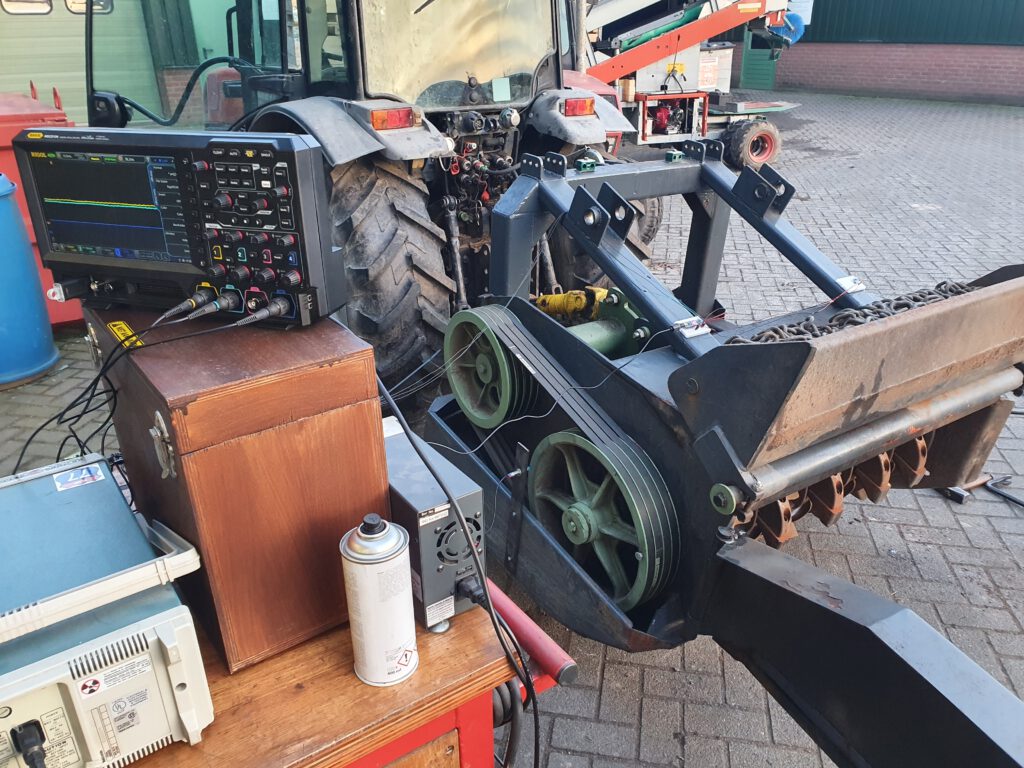
Because i am an Mechatronic Engineer i got a proper Oscilloscope so i got that out and started thinking how to do this. When i know the position of the axle and the acceleration of the Z-axis in time i know where the drum is too heavy. Because the machine has a left and right wobble i needed multiple sensors to measure the unbalance properly. I decided to do a test with the 2 accelerometers and a inductive sensor to determine the “zero” postion. The “zero” position is measured by drilling a hole into the axis drive pulley and adding a small bolt here. This measured the “zero” position on the oscilloscope with a peak which i could trigger nicely. Measuring out both accelerometers during rotation gave me a very clear image of the vibration left and right and straight away visualised the actual wobble issue.
At just 600 rpm on the drum of the buschmulcher it already showed accelerations of 300mv which translates into over 3G which is way too much for a 1200kg weighing machine!
The yellow probe samples the left side of the machine.
The blue probe the right side of the machine.
The dark blue probe samples the “zero” pulse.
With that knowledge we can clearly see that left and right side have a 180 degree phase shift in the acceleration meaning that they accelerate exactly opposite and this is what’s causing the left/right wobble.
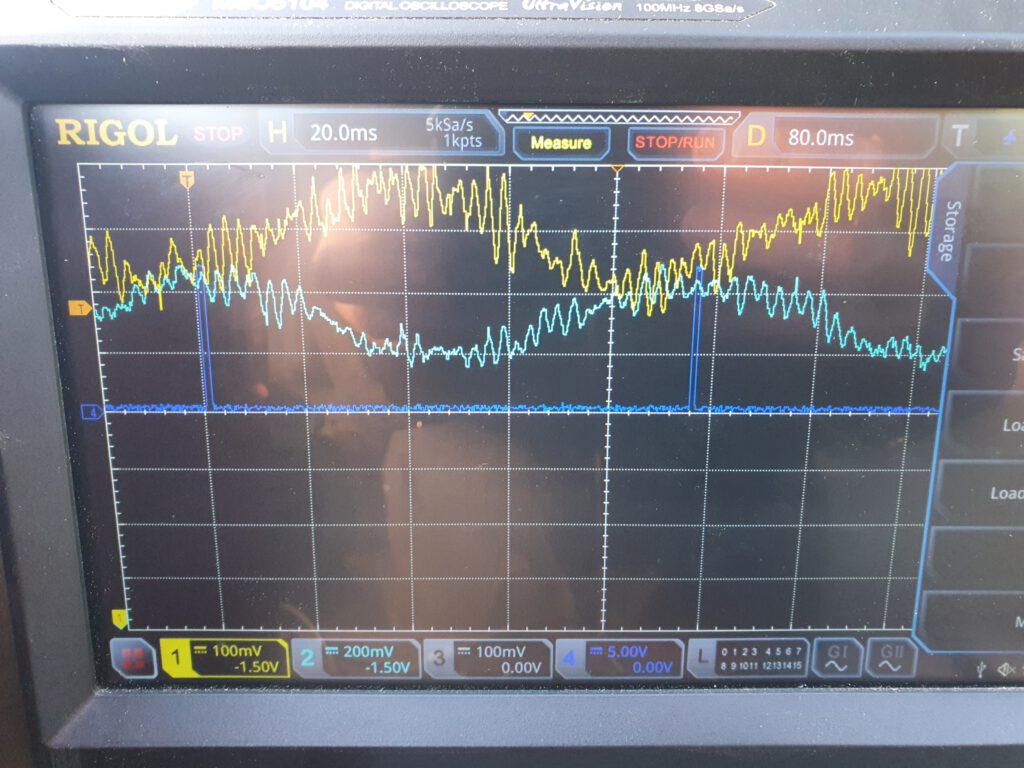
Now to fix this unbalance i have to weld in metal weight. Because the drum itself is already 400kg and i got this much unbalance i start by adding metal pieces of 1kg, i can’t really fit much bigger pieces in there at once. I tack weld the part in each time and do a testrun again.
To determine the position to weld for left or right i look at the acceleration spike on the scope, i rotate the drum to sense the 0 position. then add my offset of the “zero” position to the peak position which makes me know in that position the peak is on top of the drum, and i need to weld on the bottom of the drum. i rotate it another 90 degrees to know the place to weld for the left side is on the rearside.
By doing these steps i knew i was welding correctly and i could also see and feel improvement by every weight i added.
Eventually i added over 20kg of metal in the machine with about 10kg on the left side and 10kg on the right side with a 180 degree phase shift.
I did so by everytime i had it balanced until a specific rpm to go up a bit higher and see the peaks increase with that higher rpm.
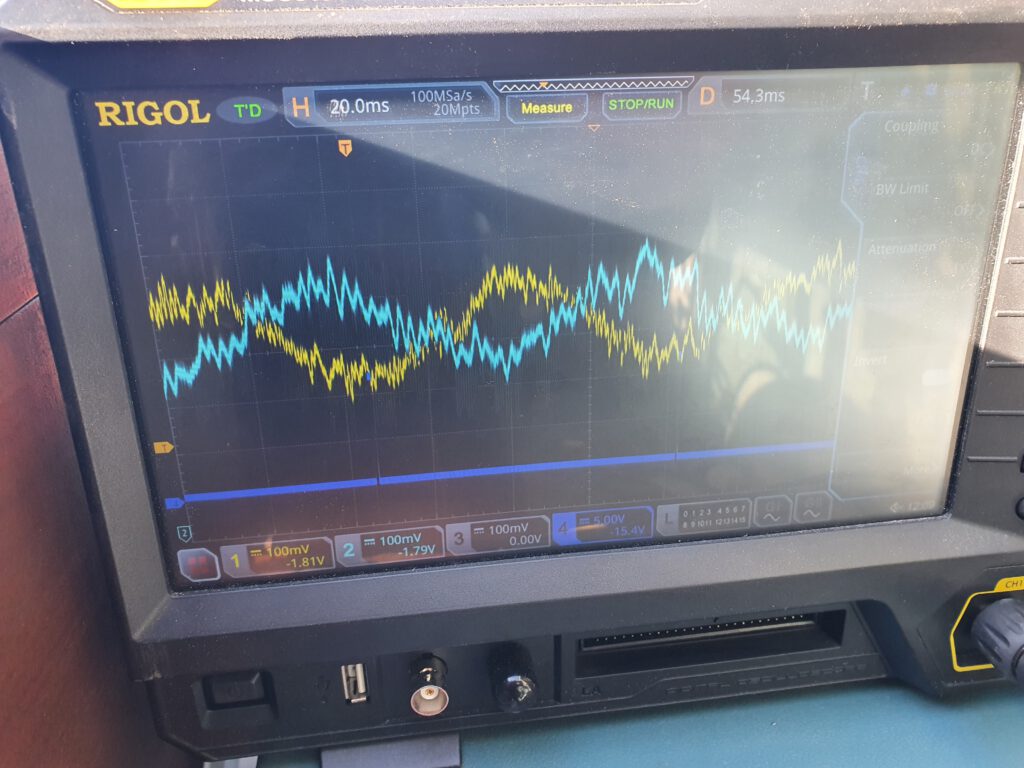
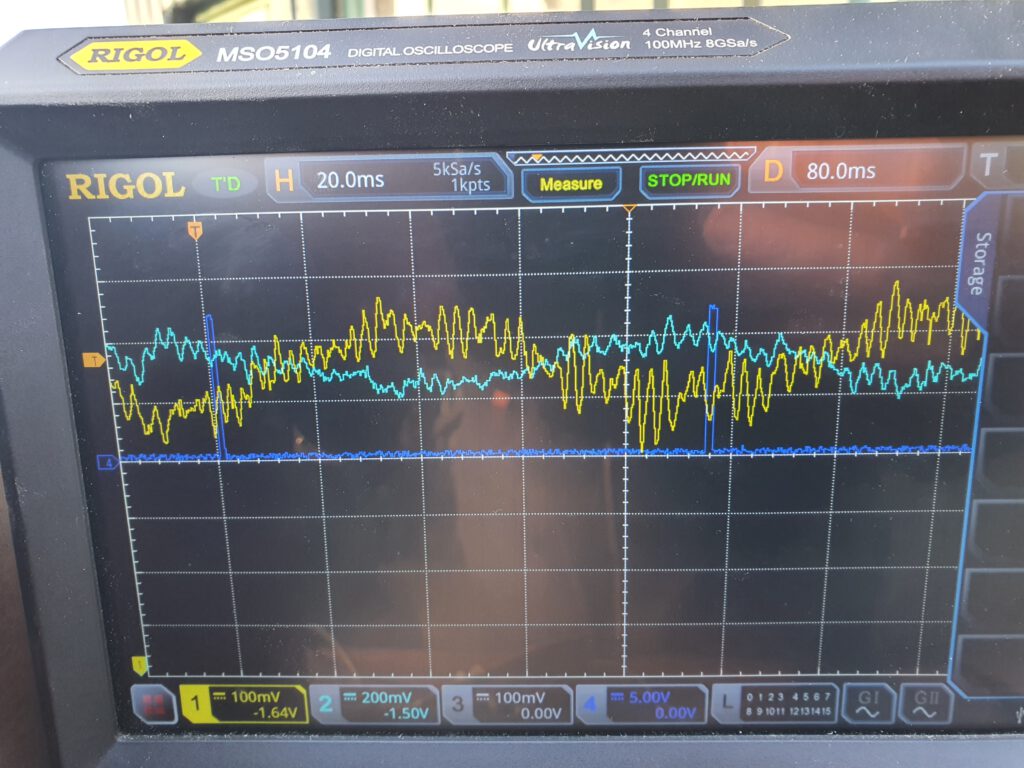
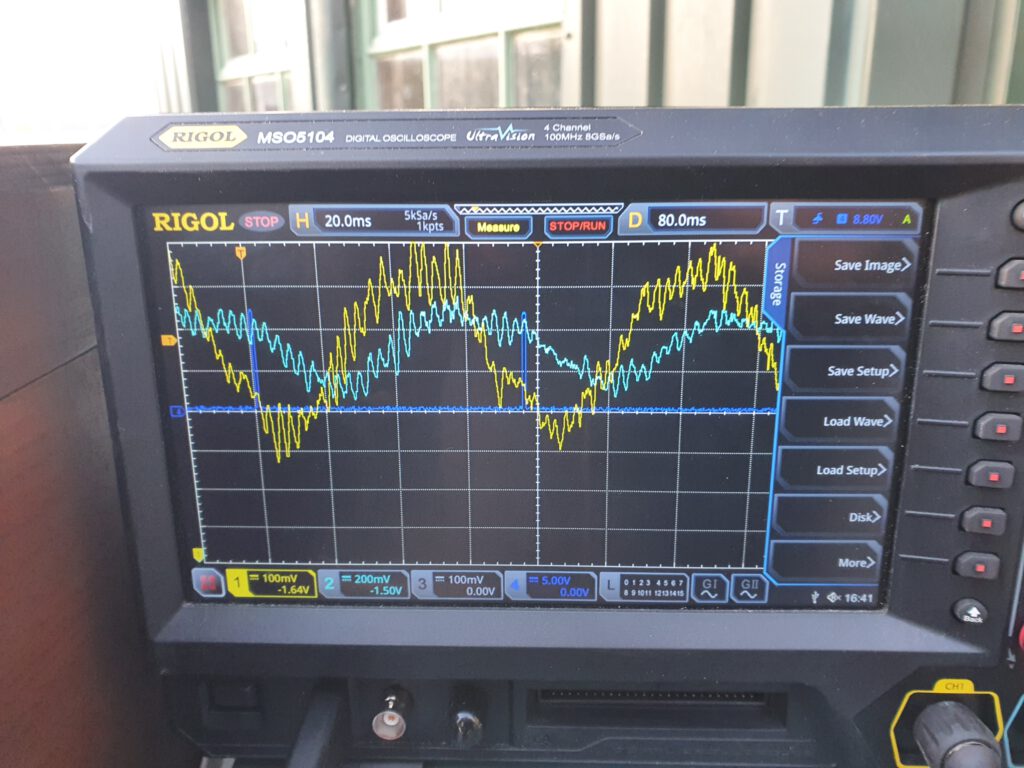
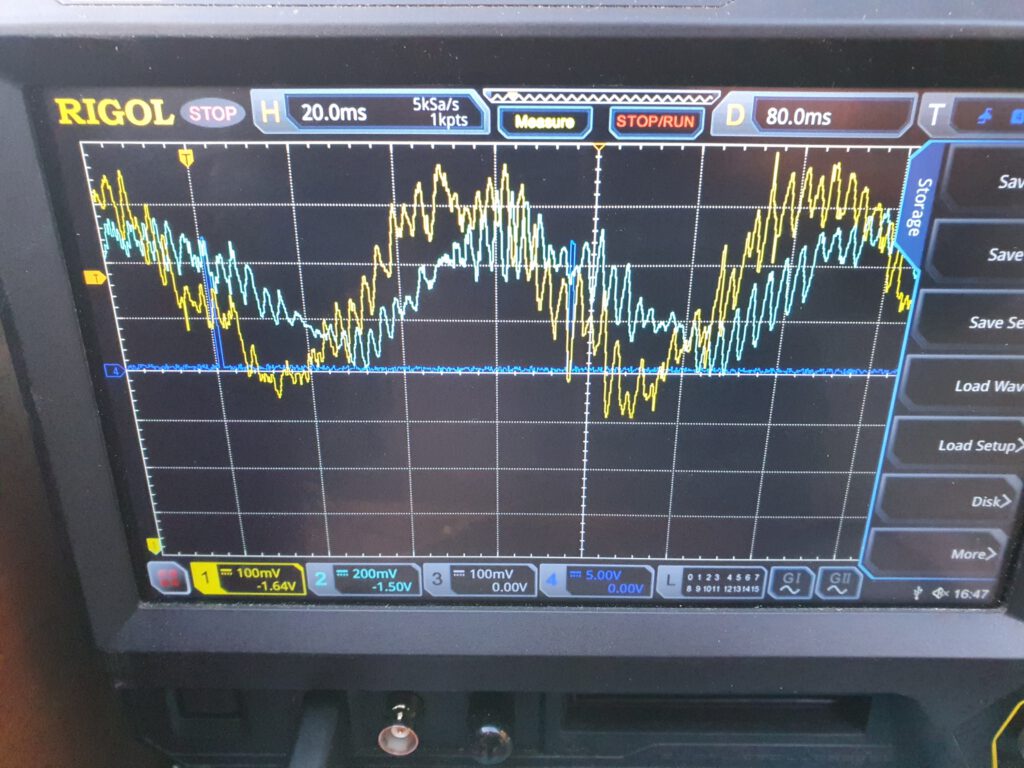
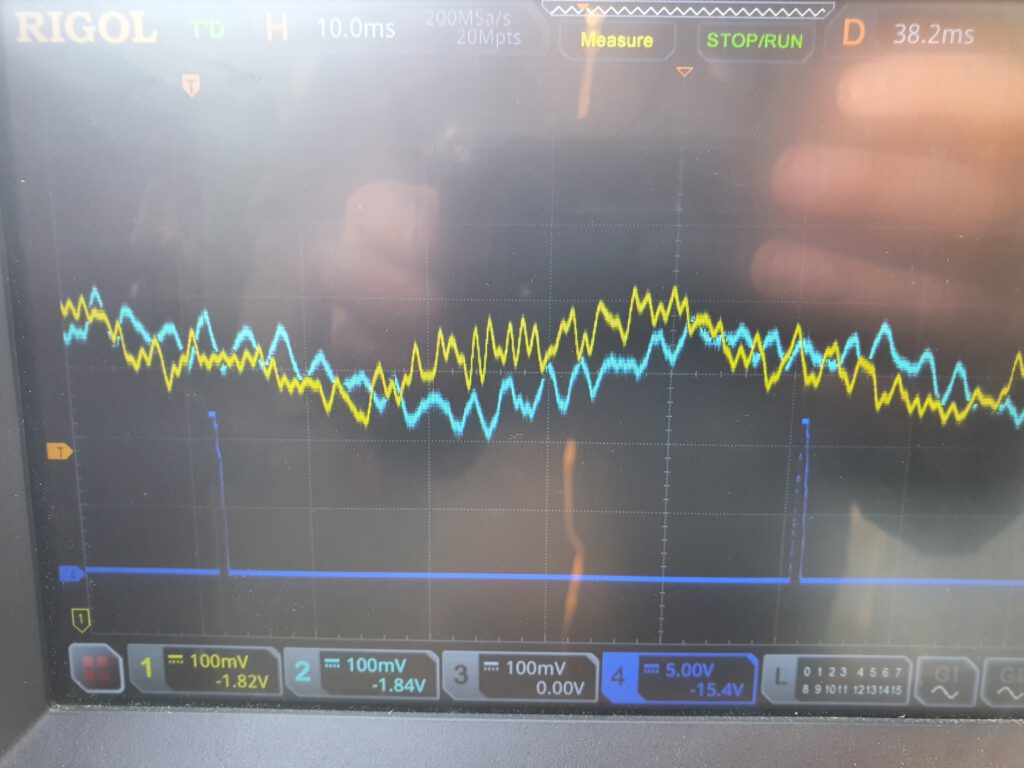
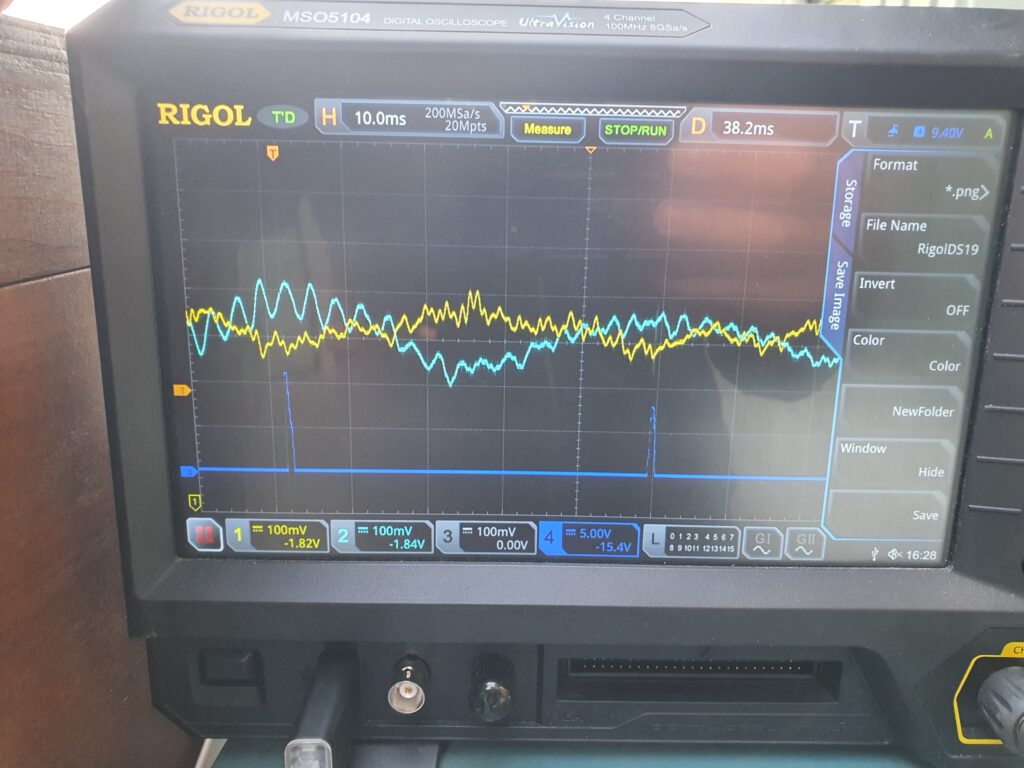
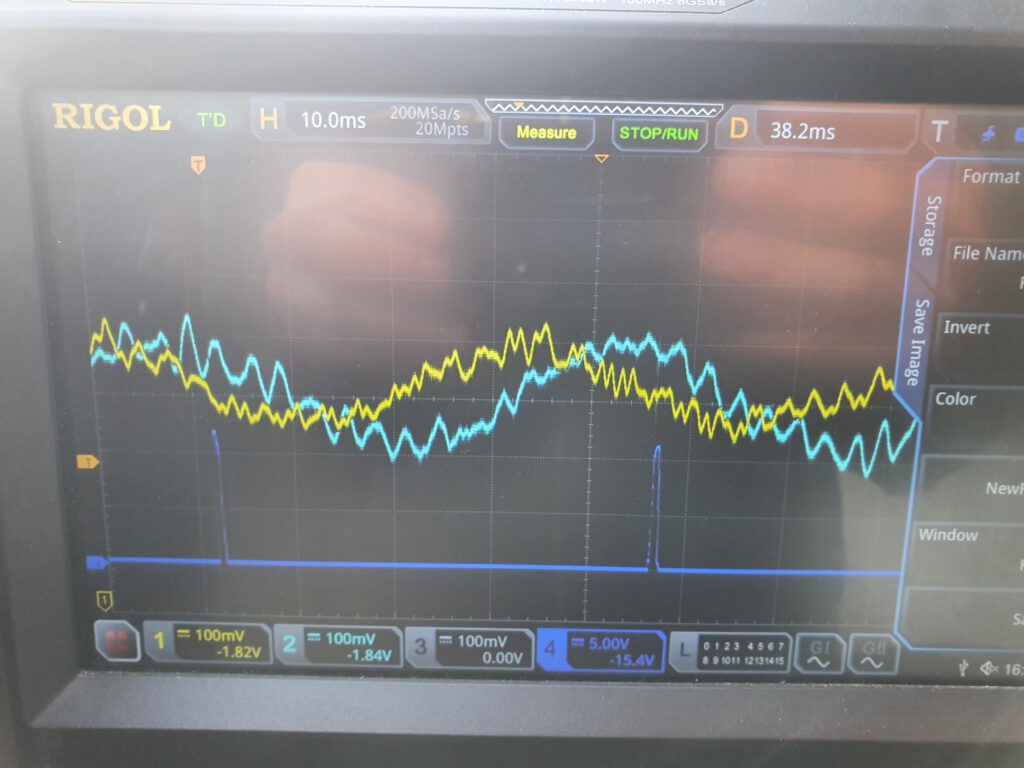
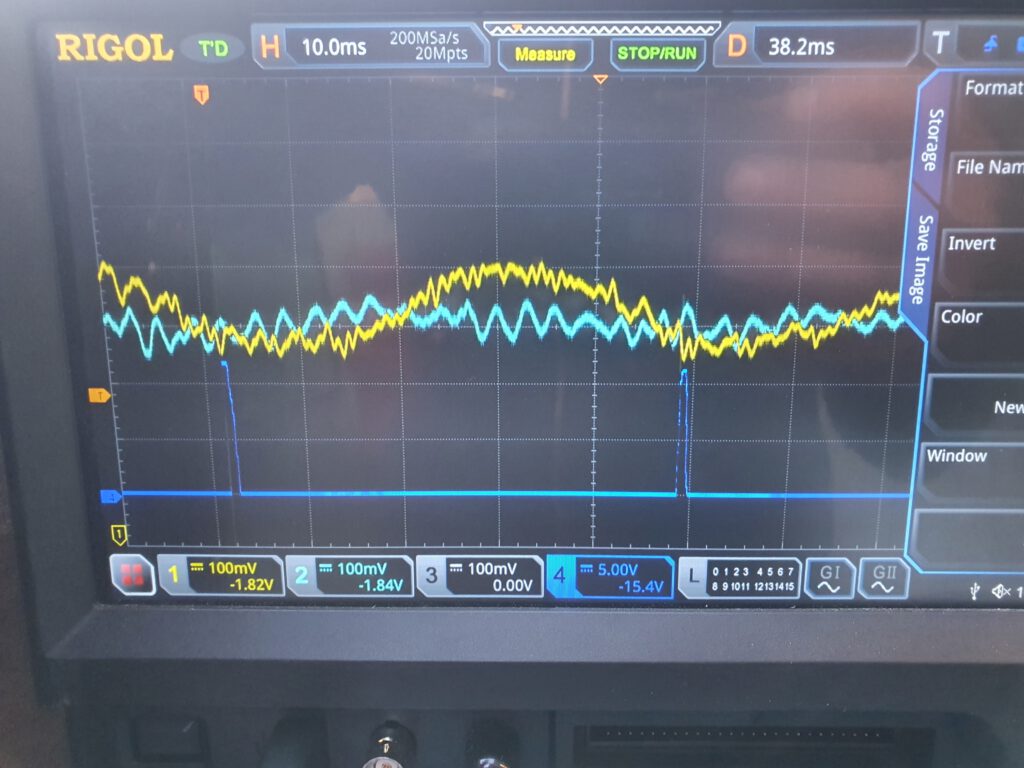
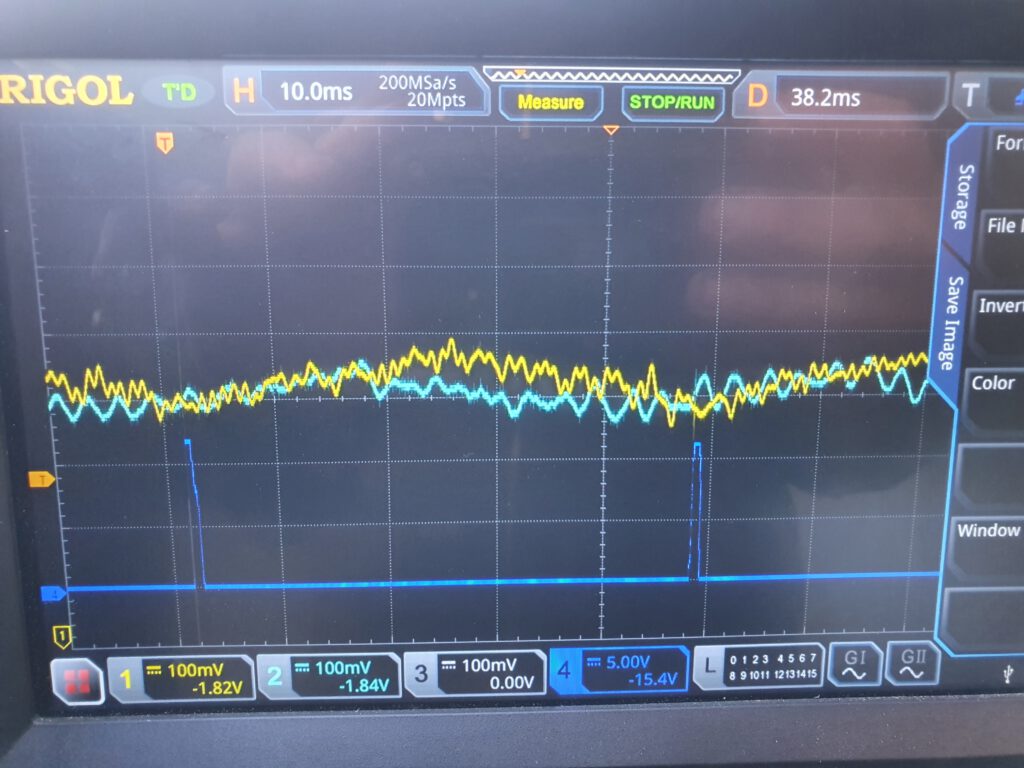
After getting the machine balanced on it’s last 20 grams i was able to swing it up to it’s full 2200 rpm on the drum with 1200rpm on the PTO.
The machine now sounded perfect, the tractor showed no vibrations at all and you couldn’t tell from the cab if it was running or not. having it run this nice with the work i had to get it balanced was worth all the effort!
And now get this machine to work again in the orchard!
Balancing the Bush Mulcher
Click here to display content from YouTube.
Learn more in YouTube’s privacy policy.